Simulation-Driven Innovation for the Energy Industry
Our solutions support power generation, renewable energy, and grid infrastructure, providing you with the tools and expertise needed to tackle complex engineering challenges. From engineering simulation software to expert consulting and testing services, SimuTech Group helps energy companies optimize performance, enhance reliability, and reduce operational costs.
Ready to take your energy systems to the next level? Our team is here to provide tailored simulation solutions. Connect with our experts today to discuss your specific needs and challenges.
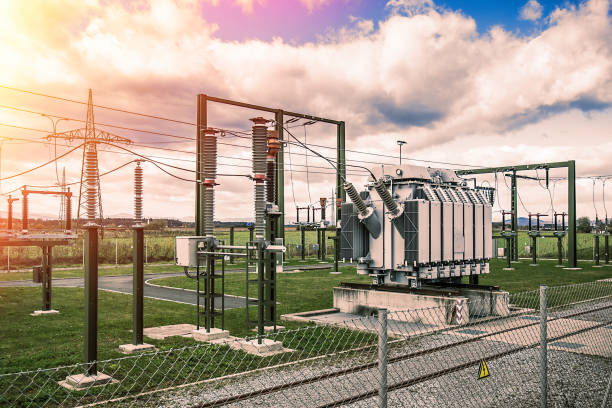
Request an Energy Systems Consultation
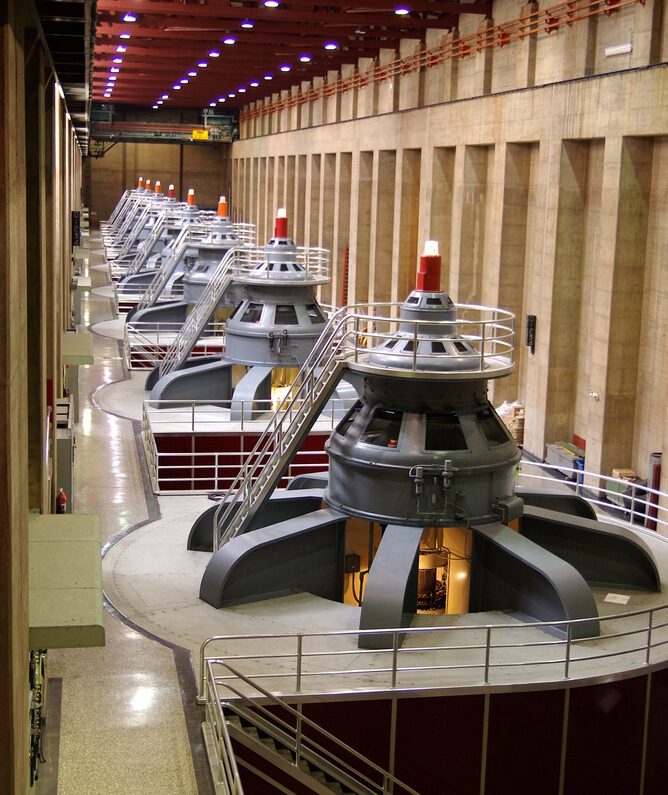
Engineering Simulation for Advanced Energy Systems
As the energy industry evolves, your need for optimized performance, efficiency, and reliability across power systems becomes crucial. At SimuTech Group, we provide the expertise, software, and consulting services to help you drive innovation and solve complex engineering challenges. Whether you’re working with renewable energy sources (such as wind, hydro, and solar), smart grid technologies, or energy storage solutions, we have you covered.
Our advanced simulation solutions integrate cutting-edge technologies and methodologies to enhance the sustainability and resilience of your power generation and distribution. We specialize in structural, thermal, fluid dynamics, and electromagnetics analysis using Ansys CFD, FEA, and EMAG simulation software.
Partner with SimuTech Group to take your energy systems to the next level.
Explore Our Expertise in Energy Systems:
Wind & Hydro Power: Improve turbine efficiency and structural integrity
Solar Energy Systems: Optimize thermal performance and durability
Battery Storage & Grid Reliability: Enhance energy storage and distribution models
Steam Turbines & Generators: Advanced fatigue analysis and failure prevention
Heat Exchangers & Thermal Management: Increase efficiency and longevity
SimuTech Group has been a trusted partner in the energy sector for over 30 years. Contact us today to learn how our energy simulation solutions can help your projects succeed.
Key Power System Elements Optimized by Energy Simulation
Design Elements | Challenges | Simulation Benefits |
---|---|---|
Steam Turbines |
|
|
Motors & Generators |
|
|
Balance of Plant |
|
|
Transmission Systems |
|
|
We’re Here to Help
Our team of experienced engineers can assist you at any step of your process.